An In-depth Summary of Container Welding Examination Standards and Methodologies for Improved Weld Top Quality and Performance
The importance of welding inspection requirements in the production of containers can not be overstated, as they act as the foundation for making certain weld integrity and functional dependability. Numerous evaluation methods, including aesthetic analyses and advanced non-destructive screening techniques, are vital in determining prospective problems that can jeopardize efficiency. Adhering to regulatory standards not only enhances weld top quality however also mitigates the risk of pricey failures. As we discover the nuances of these methods, it becomes imperative to think about exactly how an organized method can revolutionize present practices and bring about significant enhancements in results.
Value of Welding Inspection Criteria
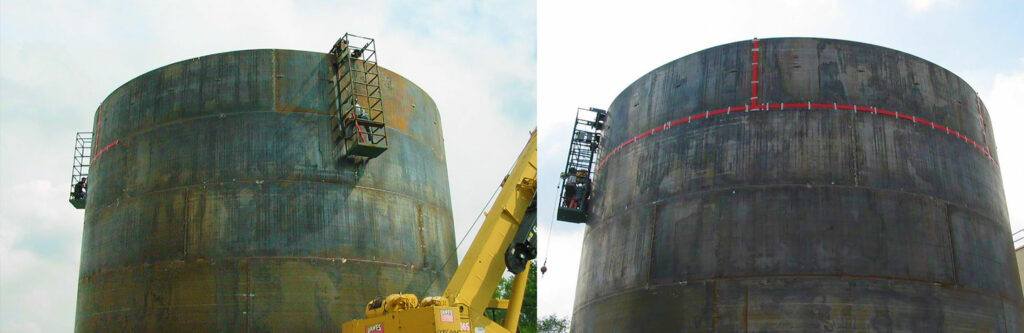
Welding assessment standards incorporate a series of standards, including material specs, welding procedures, and qualifications of employees involved in the welding process. By applying these requirements, organizations can methodically recognize and fix possible issues, therefore minimizing the possibility of costly fixings or disastrous failings. Rigorous evaluation techniques foster a society of responsibility and precision, encouraging welders to maintain high degrees of workmanship.
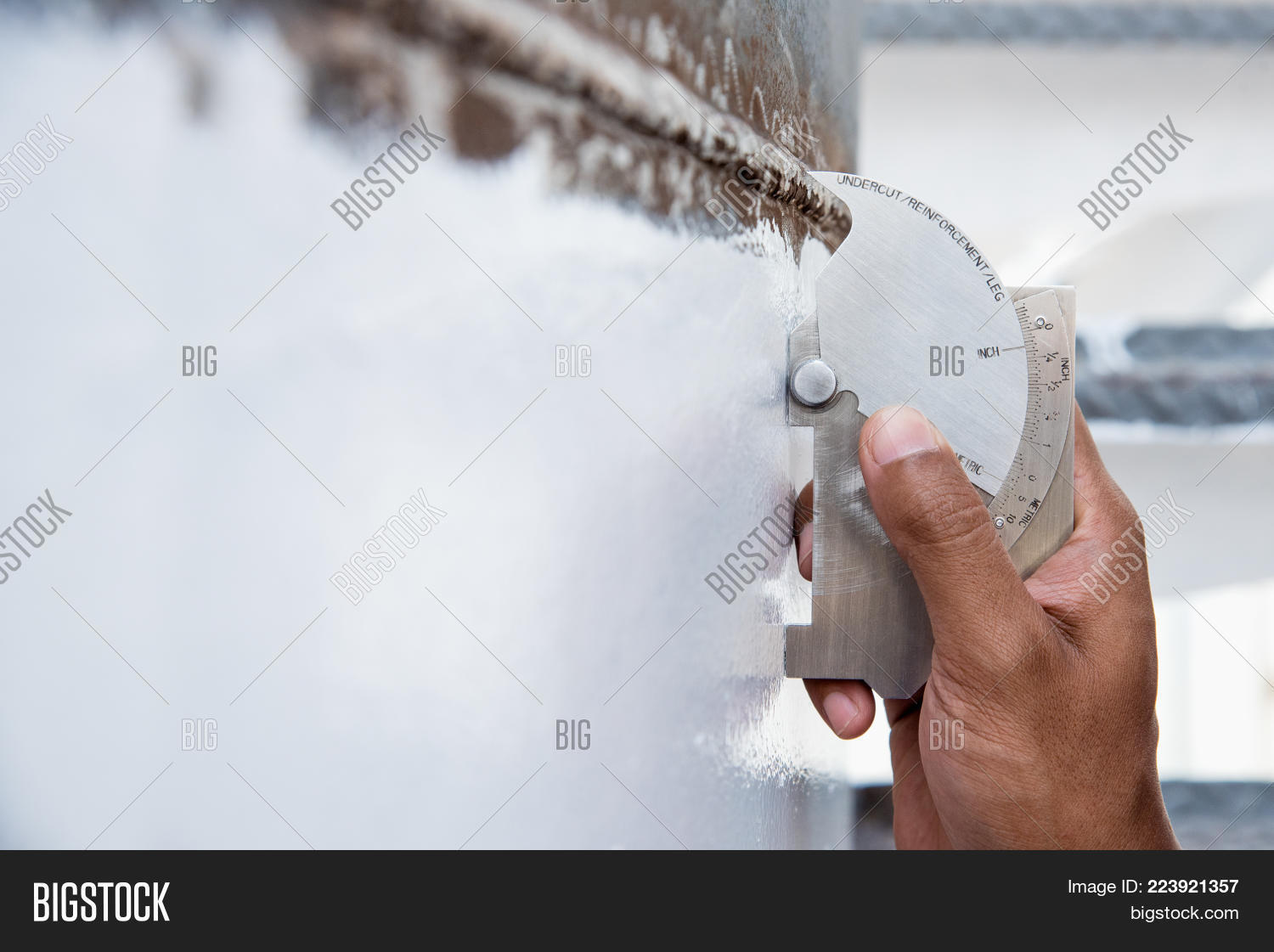
Usual Welding Assessment Strategies
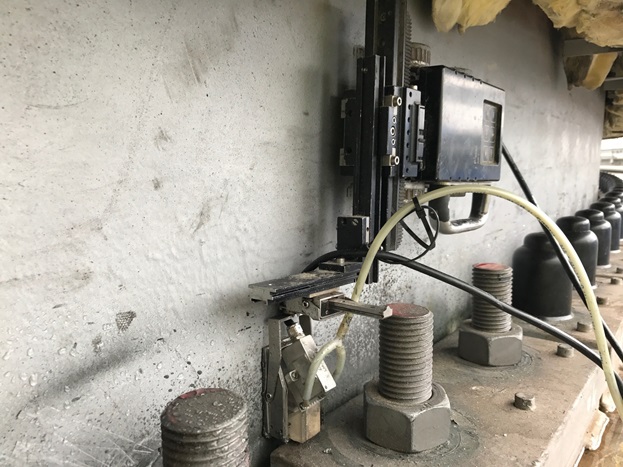

Ultrasonic Evaluating (UT) is another prevalent strategy, using high-frequency sound waves to detect interior defects that might not show up on the surface. This approach is especially efficient for recognizing spaces or inclusions within the weld metal. Magnetic Fragment Evaluating (MT) is additionally commonly made use of, specifically for ferromagnetic materials, as it exposes surface and near-surface defects via the application of electromagnetic fields and ferrous bits.
Additionally, Liquid Penetrant Screening (PT) detects surface-breaking problems by applying a penetrant to the weld and then using a developer to extract the penetrant. Each of these techniques contributes to a comprehensive inspection approach, guaranteeing that welds satisfy the rigid quality requirements called for in storage tank building and construction.
Governing Requirements and Compliance
Governing criteria and compliance are important parts in ensuring the safety and integrity of bonded structures in storage tank building - Tank Welding Inspection. These standards offer to establish minimum needs for material homes, welding treatments, and examination techniques, thereby minimizing the risk of architectural failings and improving overall efficiency
Key organizations, such as the American Culture of Mechanical Designers (ASME) and the American Welding Culture (AWS), offer standards that are widely embraced in the sector. Conformity with these requirements not only makes certain adherence to finest methods however likewise meets lawful and contractual commitments, securing the passions of stakeholders.
Governing bodies often mandate adherence to particular codes, such as ASME Code Area IX for welding qualifications and API 650 for welded tanks. These codes lay out requirements for welding methods, qualifications of personnel, and screening approaches to confirm weld integrity.
Normal audits and assessments are crucial to keeping conformity, as they assist identify deviations from established requirements. Non-compliance can cause considerable penalties, task hold-ups, and safety risks. Therefore, a robust understanding of governing requirements and a commitment to compliance are extremely important in achieving top quality and sturdy welded container structures.
Non-Destructive Checking Methods
Exactly how can the stability of bonded frameworks be guaranteed without triggering damages? Non-destructive testing (NDT) methods use a durable service, allowing examiners to review weld quality without compromising the product - Tank Welding Inspection. Amongst the most typical NDT strategies are ultrasonic screening (UT), radiographic testing (RT), magnetic bit testing (MT), and color penetrant screening (PT)
Radiographic testing involves passing X-rays or gamma rays via the weld, developing images that reveal architectural issues such as splits or gaps. This technique is indispensable for analyzing the integrity of complicated welds.
Magnetic fragment testing is fit for ferromagnetic products, where electromagnetic fields expose surface area and near-surface gaps. Color penetrant screening makes use of a fluid color to highlight surface-breaking imperfections, making it an efficient approach for non-porous products.
Each of these NDT more info here approaches has unique benefits, enabling for thorough assessments customized to particular products and welding processes. By applying these strategies, markets can make certain the integrity and security of welded frameworks, inevitably boosting total performance.
Enhancing Weld Top Quality With Inspection
Efficient inspection plays a vital role in enhancing weld quality, working as an important checkpoint in the fabrication process. By determining possible problems early, inspections alleviate the threat of compromised architectural stability and ensure conformity with sector criteria. Utilizing a combination of visual evaluations, non-destructive testing (NDT) methods, and mechanical evaluations, assessors can identify concerns such as porosity, cracks, and insufficient blend.
Implementing a robust inspection protocol not just enhances the overall quality of welds but additionally cultivates a society of responsibility among welders and producers. Routine training and qualification of examination employees make sure that they are equipped with the essential skills to acknowledge and attend to prospective issues properly. This aggressive technique lessens rework and linked expenses, inevitably adding why not try these out to predict effectiveness.
Furthermore, detailed paperwork of inspection searchings for provides beneficial understandings into reoccuring concerns, promoting special info continuous improvement in welding methods. By leveraging advanced innovations, such as automated ultrasonic screening or digital radiography, weld high quality can be boosted through much more precise examinations. Finally, a strenuous inspection process is important in attaining premium welds, guaranteeing safety, integrity, and durability in container construction.
Verdict
In verdict, the implementation of strenuous container welding assessment standards and methods is vital for making sure weld stability and performance. By utilizing a combination of aesthetic examinations, non-destructive screening methods, and adherence to regulatory criteria, organizations can effectively recognize and mitigate prospective defects.
Comments on “Comprehensive Overview to Tank Welding Inspection for Safety and High quality”